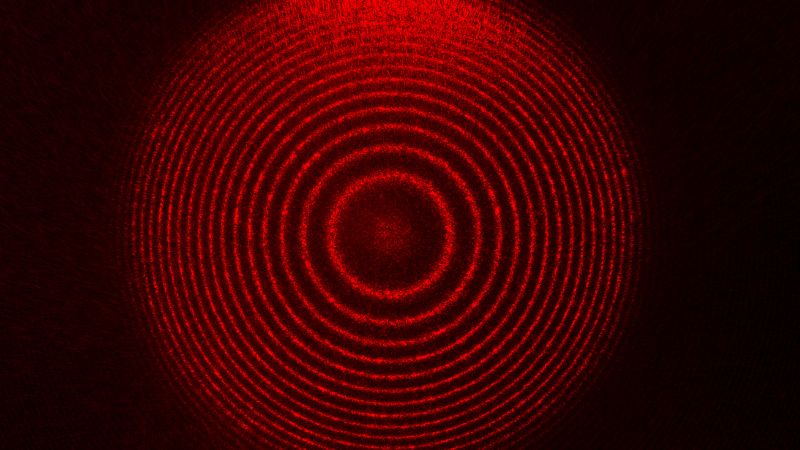
Tools, Tech, Transformation – a National Industries Info Series
When it comes to the latest tech and developments in metal fab – and all things related – there’s no denying our team is just a little bit obsessed. If there’s new equipment hitting the market, ground breaking techniques being showcased or an AI integration being tested, you better believe it has our attention.
Lucky for us, a lot of the clients we work with – from engineers to technicians, industrial procurement to QAs – share our interest in these areas. With that shared passion in mind, we thought… Why not explore the ways equipment just like ours is being used throughout the world (and beyond), in mind-blowing ways?
So, get ready for the countdown, as our first Triple T Series article takes off!
For all mankind
In 2015, a little space movie starring Matt Damon hit screens and made a bit of a splash. You might remember it – a team of astronauts is sent to Mars on an exploration mission, and after a severe dust storm, where one of the team is presumed dead, they realise, actually, they’ve accidentally just left their mate behind.
Cue Damon – a botanist and mechanical engineer – desperately trying to survive on the inhospitable planet, until his colleagues can make the dangerous return to pick him up.
If you’re a bit of a space enthusiast like some of us here, you know there were a few problematic ‘as-if’ moments in this movie. Perhaps more important though than its scientific accuracy, there was also the mainstream reintroduction of the dream that we, as humans, can one day permanently live on Mars.
As you will likely know, in the last ten years, we’ve made giant leaps towards that dream becoming a reality, as both NASA exploration of Mars lurched forward, and more commercial space operations kicked into gear.
Needing no introduction (for various reasons), Elon Musk has been a leader in the conversation, setting his visionary sights and plentiful funding on the SpaceX Mars Colonisation Program (Occupy Mars), with a goal to have a crewed mission to the planet as early as 2029, and a self-sustaining colony underway by 2050.
Though 2050 might seem light years away, that 26 years will go incredibly quickly, and as such, work towards meeting that goal is well underway and ramping up to warp speed!
So, what’s all this got to do with laser, and especially our area of specialisation, laser cutting? Well, the answer is… everything!
Lasers are almost out of this world
While some of the obvious elements that are holding us back from living on Mars are quite literally ‘elements’ – oxygen and water supply, radiation and an atmosphere that can’t protect us – a key factor is also infrastructure, the ability to build and maintain it… and how long it takes to send back to earth for the specific spare parts that keep it working (around 500 days right now).
And that brings us to metal fab and laser cutting.
Back down here on Earth, most days at National Industries are spent using laser cutting and metal fab to produce components that go in everything. We output parts for cars and communication devices, ag tools and springs, and in a chicken-and-egg-type scenario, the parts that also make laser cutters (which came first?!?).
Laser cutting has advanced significantly over the last few decades, with the level of accuracy skyrocketing, and productivity – its ability to produce parts quickly – beyond anything imaginable when we started our business 60 years ago. Inhouse now, we have laser cutting devices that can produce thousands of components each day, fulfilling orders in record time, with minimal manual intervention.
Obviously the opportunity to produce components like this, in space, will be a fairly crucial part of becoming self-sustainable.
Once ‘up’ there, however, a lack of air to dissipate heat, the lack of ability to contain and control assist gasses like oxygen and nitrogen, and those pesky molten cut offs, among other issues, mean laser cutting hasn’t really had its opportunity to shine yet, unlike lasers used in communication and the mapping of planetary surfaces.
What’s the difference between the two? Well, even though lasers in all applications essentially come from the same place, monochromatic light, there are a lot of differences.
Lasers used for applications like communication are high quality, and they typically operate in the infrared wavelength (around 1.3 to 1.55 micrometers), with low power, don’t require cooling, and come in at a lower cost.
In contrast, cutting lasers operate at various wavelengths depending on the material being cut, focus on one concentrated spot, generating a lot of heat, and can be quite high-cost. These factors mean right now, laser cutting might not excel in space.
Pre-count-down and take-off though, laser cutters have already played a prominent role in creating the precision parts needed for spacecraft and exploration vehicles like the Mars Rover.
Everything from the frames and outer structure, to heat shields and thermal insulation tiles, and components like nozzles and combustion chambers in propulsion systems have benefited from accurate laser cutting in their manufacture.
And while for us, the approach to this work alone and the resulting components is exciting enough, what’s really interesting is what has been earmarked for laser cutters in the future of space.
Space: the new laser cutting frontier
It might seem overly simplified to talk about laser cutting and its role in space – like there are a lot bigger and more important players in the game. But the fact is, our job and our passion at National Industries is to always think about all the components, how something is made, how it can work, and how we can innovate to make it better.
In that sense, thinking about how we can efficiently and accurately produce spare parts for vehicles in space, as an example, is right up our alley and not a strange thing for us to chat about at lunch time!
It seems, however, we aren’t alone in that thinking, with scientists, researchers and engineers already laser focused on how to use this technology for our advancement in space.
Removal of space debris
That scene in every space travel movie, when debris starts to rain ‘down’ on our heroes and asteroid showers threaten to break their ship into smithereens – you all know it – is obviously exciting on the big screen; but in real life… no thanks!
Managing space junk and debris has already been identified as an important area for development in space travel, with organisations like the European Space Operations Centre (ESOC) using a system known as the Space Debris Telescope, which employs lasers to track the position and trajectory of space debris. While the information is vital for avoiding collisions and planning safe satellite operation, there’s much more to come!
Scientists have begun to explore the use of lasers to cut up space debris, altering its trajectory, and causing it to move off course or re-enter the atmosphere and burn up. And while this might all sound a little ‘Space Force’, the reality is, it could be a matter of life and death both as space travel expands in the future, and when one day, that big rock does inevitably hurtle towards us!
Mining for resources
Already in the research phase on earth, and sure to be useful in Elon’s colony on Mars, laser has the potential to be used in place of explosives when cutting and blasting through rock to find and extract resources during mining.
In 2020, one US company developed a prototype that identifies and breaks down volcanic rock formations containing narrow veins of precious minerals. This type of application could allow for much more precision mining, resulting in less damage to the environment around it, and higher levels of productivity.
– – –
With this year fast coming to an end, and Musk’s first goal of sending a human crew to Mars not far away, the inner child in all of us still hopes to one day get the call to be part of a mission, but for right now, we’ve got exactly what it takes to create the parts that will get everyone else there, and that’s good enough!